Watches & Wonders 2025: A Visit To The Tudor Manufacture In Le Locle
Unsurprisingly, Tudor’s high precision watches are the product of a high precision operation.
Tudor historically made use of movements obtained from external suppliers but starting in 2015, the company launched its first in house movement, caliber MT5621, in the North Flag, and in another major step, began producing movements to the Master Chronometer specification, which will eventually be applied to all Tudor watches.
Master Chronometer certification is carried out by METAS, the Swiss Federal Institute of Metrology. Master Chronometer certified watches must be “Swiss Made”; certified as chronometers by the COSC; they are tested at two different temperatures in six different positions, and at two different points in the power reserve (100% and 33%); they must run within 0/+5 seconds maximum deviation in rate per day; power reserve is verified to be in accordance with the manufacturer’s claims and most notably, a Master Chronometer must be able to function after exposure to a magnetic field of 15,000 gauss (for comparison, the permanent magnets inside an MRI machine are usually between 0.5 to 1.5 tesla in strength, or 5000 to 15,000 gauss).
Tudor watch movements are manufactured at Kenissi, which is adjacent to the Tudor factory in Le Locle. Kenissi began in 2010 as a project to bring movement manufacturing in-house at Tudor, but Kenissi also functions to some extent as an independent supplier, providing movements to among others, Breitling, Norquain, Chanel (which has a 20% stake in Kenissi) Fortis, and of course, Tudor.
A visit to the Tudor factory, if you are coming from Geneva, means about an hour and a half drive from Geneva to the town of Le Locle, which has for many decades been one of the major centers of Swiss watchmaking; on the way there you’ll drive by a number of other factories, including Cartier and Greubel Forsey. A visit to the Tudor factory starts in a reception room dominated by a large, glass-topped table inside of which are a sampling of vintage and modern Tudor watches, as well as a model of the Tudor and Kenissi factories.
The two buildings are very similar architecturally and both have basically the same mission, which is to reliably and repeatedly produce movements capable of running within the Master Chronometer precision spec, and which when cased will be extremely reliable in terms of essentials like resistance to magnetism, power reserve, and water resistance.
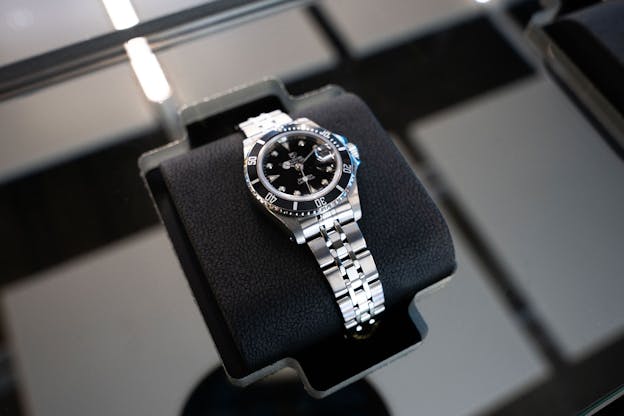
One of the first stops on the tour is, believe it or not, the basement, where the climate control system machinery is located. In order for testing results to be consistent, environmental conditions inside the building have to be consistent as well no matter what Mother Nature’s doing outside.
The entire building sits on a massive foundation of concrete pillars drilled into the bedrock of the Jura massif under the factory; humidity and temperature are kept constant as changes in either can affect movement and watch testing, and interior light is kept constant thanks to windows in the factory which become more or less translucent depending on how bright the sky is outside.
These are nitrogen cylinders, off to one side of the main machine room, which are part of the dry fire suppression system. In some parts of the factory there is a conventional sprinkler system but in other areas – the massive sealed vault where components are kept, for instance – a dry suppression system helps ensure there won’t be water damage to expensive stored components in the unlikely event a fire does occur.
Unfortunately, that sealed vault, which was one of the most interesting parts of the tour and around which the entire factory is constructed, can’t be photographed for security reasons. We were able to enter the room outside the vault itself, which is shut off behind a massive bank vault style door, and see the storage, inventory, and delivery system in action. The basic process for selecting and delivering components is called “just in time” inventory management, which in turn is part of the famous kaizen manufacturing philosophy developed in Japan after the end of World War II – it is perhaps most famously used by Toyota, which published the details of the TPS, or Toyota Production System, which was developed over the period 1948-1975. “Just in time” means “make only what is needed, only when it is needed, and only in the amount that is needed,” with a view to eliminating waste in inventory storage, manufacturing and transportation time, and processing. Just in time is accompanied in the TPS system with “jidoka” which means “automation with a human touch,” in which high precision automation is combined with constant human observation and quality control.
When a department at the Tudor factory requires a component – hands, dials, a movement, a case, gaskets, or what have you – the order comes through as the requirement is identified, to the central distribution system just outside the vault. Inside the vault, the tray or trays pre-loaded with the necessary components is selected, removed by a robot from its location, and delivered automatically via a roller conveyor belt, to a technician who then loads the necessary components into a second delivery tray. The delivery tray then leaves the staging area and is automatically delivered to the correct location in the factory. While much of the system is automated, a human technician has final responsibility for ensuring that the right number of components are going to the right location. This human supervised quality control step is something we saw in many other processes at Tudor.
The entire kaizen based system is designed so that customer demand drives production, from the retailer all the way back up the line, through the factory assembly area, vault, and even extending back to Tudor’s next door neighbor, Kenissi.
The main assembly area is where you start to realize just how many manual processes and checks there are. Tudor, like every major or even minor watch manufacturer, relies on an enormously complex supply chain for its components, with dozens of companies contributing. Tudor is unusual in that it is a majority shareholder in several of the suppliers of what it calls strategic components, which helps ensure the reliability of its supply chain; Kenissi is one obvious example. The assembly of components in the main assembly area, however, is almost entirely done by hand. Movements are cased, hands and dials placed, and bracelets set on watches by watchmakers who carefully inspect the watches-in-progress at every step in the assembly process – the position of watch hands are checked to ensure they line up correctly; movement casing involves repeated checks to ensure no dust or other debris has entered the case; and even bracelets are attached to watch heads by hand.
The entire assembly area is under positive air pressure, so that should the giant room accidentally open to the outside air, the air will flow out, rather than in, avoiding the possibility of dust contamination.
If like so many enthusiasts you have struggled with spring bars at 2AM, you would be astounded at the speed with which the technicians at Tudor can fix bracelets to watch heads. It goes without saying that this work has to be done with great care, since scratching a case by accident will bring the entire assembly process to a halt.
In order to avoid time wasted in getting components to and from locations where they’re needed, Tudor employs these little guys – industrial robots who will get what’s necessary where it has to go. The robots have a collision avoidance system and if a visitor (say, a watch journalist) happens to blunder into their path, they will politely wait for the obstacle to remove itself.
This is also where machinery for Master Chronometer testing can be found.
This massive permanent magnet has a tunnel running through its center, through which watches are passed as part of the Master Chronometer testing process. The magnet is so heavy that it requires its own structural supports in addition to the supports in the main floor. After being passed through the magnet, assembled watches are then sent for precision testing.
Another step in the Master Chronometer certification process, is water resistance testing.
Each one of the enormous pressure vessels inside the test chamber can generate internal pressures equivalent to 2000 meters of water pressure. Tudor tests all of its watches to 25% over the stated water resistance; the new Tudor Pelagos Ultra, for instance, is rated to 1000 meters, but tested to 1250 meters.
METAS, by the way, conducts its own controls on Master Chronometer certified watches. Inside Tudor, there’s a separate METAS testing lab, to which Tudor does not have access; it’s there, with its own dedicated testing equipment, that METAS checks watches chosen from the production line for adherence to Master Chronometer standards.
The next stop was a walk across the parking lot to the entrance to Kenissi. There is no direct access from Kenissi to Tudor and vice versa – partly because every movement Kenissi manufactures has to go to the COSC. The COSC has three labs in Switzerland – in St. Imier, Bienne, and Le Locle and the labs are equipped with atomic clocks used to benchmark the precision tests.
Kenissi’s production is very tightly focused: three different movements, all automatic, all capable of undergoing certification as chronometers by the COSC. The movements are designed to be robust, accurate, easy to service, and reliable and above all, to meet high standards for precision. Kenissi submits all its movements to the COSC for certification and the failure rate is extremely low (“much less than three per cent” we were told) and any movement that doesn’t pass the first time around returns to Kenissi for adjustment and sent back to the COSC, at which point the pass rate is basically 100 per cent. We were told while we were there that there are currently no plans to produce hand wound Kenissi movements, such movements being very much a niche product in modern watchmaking, and especially in modern industrial-scale watchmaking.
Movement manufacturing at Kenissi – the name is from the Greek “kinesis,” which means, appropriately enough, movement or motion – is like watch assembly at Tudor, a combination of manual and automatic processes. Movements at various stages of assembly move through a conveyor belt system from one watchmaker’s station to the next, ensuring both efficiency in production, and adherence to strict quality controls throughout.
Movement holders at Kenissi have embedded RFID tags, which allow exact monitoring of the position of every movement in the assembly process, as well as rapid diagnosis and correction of any problems that might arise as components gradually become completed movements.
Completed movements next go for their first chronometry test. This apparatus performs an acoustic analysis of the sounds produced as a movement ticks, to determine things like instantaneous rate, beat error, and mean daily rate; if you’ve ever had a chance to play with one, it basically works the same way as a Witschi Chronomaster.
The final step in the process is preparing the movement for testing at the COSC.
In contrast to the testing apparatus at Kenissi, testing at the COSC is visual, which means movements have to be equipped with a uniform dial so that optical checks can be made on the position of the test hand. For mechanical watches, COSC testing runs for fifteen days, 7 days a week, 24 hours a day. Once the movement has passed, it goes back to Kenissi for a final check, and then either goes across the way to Tudor, or to one of Kenissi’s other clients.
The rigor of the testing processes at Kenissi and Tudor are remarkable. Every Tudor watch goes through an initial movement check at Kenissi, fifteen days of testing at the COSC, a final movement check at Kenissi, Master Chronometer certification at Tudor, and a final control for precision before being shipped.
To some folks, this is not the sexy side of watchmaking – no gentian wood burnishing tools, no carefully applied anglage, no sharp inner corners. But this type of watchmaking is in fact, the backbone of the Swiss watch industry. The creation of watches to a high standard of precision can be done by hand, if you don’t mind taking infinite pains and an indefinite amount of time, but producing watches to better than the international standard for chronometers, at volume, and moreover at a price which is consumer friendly, is its own sort of miracle. It requires the utmost rigor and efficiency every step of the way, but it also requires constant human vigilance, in order to ensure that every time a Tudor watch is delivered, it measures up to one of the highest collective groups of standards in the business.
The 1916 Company is proud to be an authorized retailer of Tudor watches.