Introducing The Grand Seiko ‘Katana’ US Exclusive Spring Drives
An ode to the alchemy of steel.
The first time I visited Japan, it was on a trip organized by Grand Seiko for press just after the brand had relaunched internationally in 2010. Going to Japan for the first time is I think apt to be a memorable experience no matter how you slice it, but to say we came back with memories for a lifetime is to say nothing at all. One very vivid memory I have was of a visit to the watch and clock museum in Suwa City, which has in its courtyard a full-sized, working replica of the astronomical water clock that Su Song designed and had built in 1094, which had a very sophisticated constant force escapement (watching it in operation made my hair stand on end, and would even today, although there is slightly less hair now to do the standing). The Shinto shrine at Suwa was a place of immense beauty and spiritual power, enough to stir the heart of even the most hard-hearted pragmatist.
However, it was back in Tokyo on the last day of the trip, that I saw something I’d wished to see for many years but never thought I’d witness in person: the creation of a Japanese sword, at the forge of swordmaker Yoshindo Yoshihara, who has been called the greatest swordmaker in Japan. Yoshihara makes his swords the old fashioned way, using steel made from so-called “iron sand” or satetsu, which is sand mixed with iron ore – techniques for turning this material into good quality steel originally developed thanks to the relative rarity of iron ore in Japan and the method dates back as far as the sixth century. The satetsu used for swords comes from Shimane Prefecture, which, I have read, is the second least populated prefecture in Japan. The steel bloom produced from the satetsu furnace is called kera and from this the actual steel suitable for beginning the swordmaking process is refined – this steel is known as tamahagane, or “jewel steel.”
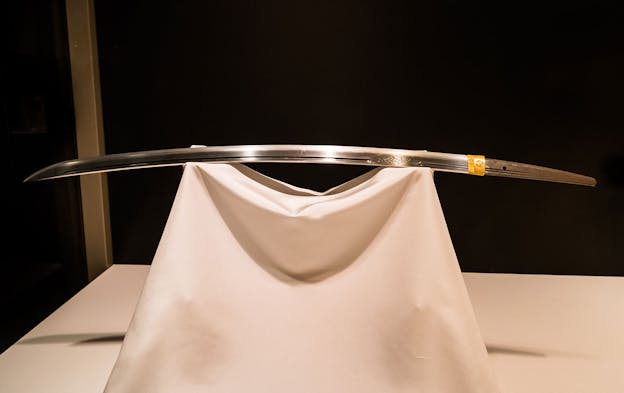
Production of this artisanal steel ceased during the Taisho period however, it was revived in 1977 by The Society for Preservation of Japanese Art Swords and today the Society, with Hitachi Metals, produces a small amount of tamahagane steel for the use of Japan’s small number of master swordsmiths.
Tamahagane during the sword-making process, is further refined into two basic sub types. These are kawagane, which is used for the edge of the sword, and hocho-tetsu, which is used for the shingane, or core of the blade. The different metallurgy of these types of steel allow their crystal structure to be optimized during the forging process for the best combination of flexibility and sharpness – smaller steel crystals appear in the edge of the sword, allowing for razor sharpness, but such a crystal structure is too brittle for the core of the sword, for which larger crystals are needed. The most well known part of the forging process is the folding of the steel billet that will become the sword, into itself, which is repeated many times and then the blade is quenched, after being coated with a clay slurry to control the cooling time for different parts of the sword. Sharpening, polishing, and the creation of the various mountings including the guard and scabbard, are separate crafts unto themselves and the completion of a single sword using traditional techniques can take months.
Swords, Steel, And Watchmaking
The reason that I’m going through this long-winded explanation is because to understand why Grand Seiko would produce these three new watches, it’s useful to understand the steps of production in the making of a Japanese sword, the best known form of which is the curved, single-edged blade known as the katana. which began to take on its modern form in the 14th century and which was preceded by the tachi. The katana is slightly shorter than the tachi and while the tachi was worn edge down, the katana was and is worn blade up, and to this day it is still possible to learn the art of rapidly drawing and cutting with the katana in one stroke, called iaijutsu (which is one of the fastest ways to end both an argument and a sword fight in the annals of both arguments and sword fighting).

The three new US-only watches all are designed around different aspects of the forging of the Japanese sword. SBGA489 and SBGA491 have patterned dials, reminiscent of the steel sand from which tamagahane is made; SBGA489 is specifically a call-out to kawagane steel, while SBGA491 is inspired by the more flexible, but less hard, steel used for the shingane. The third watch in the set, SBGA493, is a limited edition of 500 pieces and has a strikingly different dial from the other two watches – a brilliant red radial pattern, which is supposed to evoke the sparks which fly from the steel billet as it is being folded in the forge. All three watches are powered by the Spring Drive automatic caliber 9R65; all are 40mm x 12.5mm and all are part of the Grand Seiko heritage collection.
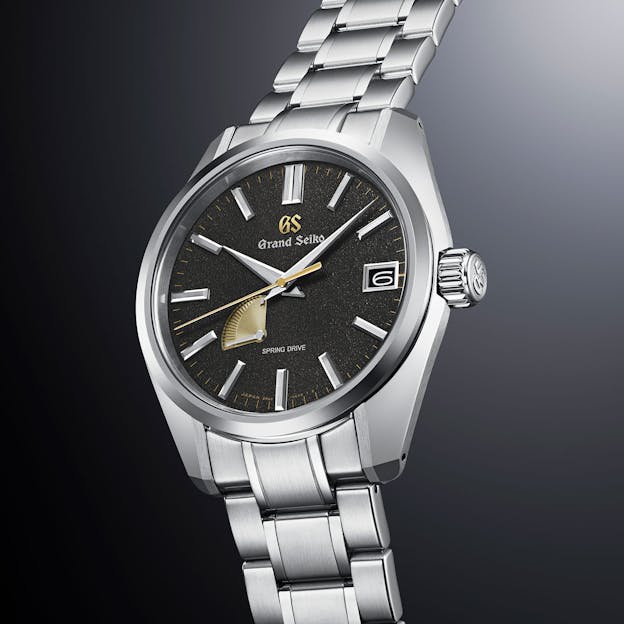
You might think that surely Grand Seiko has done watches influenced by the craftsmanship needed to create the Japanese sword before, but I don’t remember them ever specifically doing any Grand Seiko, limited edition or otherwise, which was particularly and explicitly inspired by the Japanese sword and its forging process. This type of watch is of course right out of the standard Grand Seiko playbook at this point – three hand watch with date, and a dial inspired by aspects of Japanese culture and the natural world – and there’s nothing particularly innovative about the basic concept. However, I think it’s possible to get the impression that there is less variety in Grand Seiko’s collections than actually exists. It reminds me of something a friend of mine once said, when someone asked him if he didn’t find sake monotonous compared to wine and he replied that while the flavor profile was narrower, there was still enormous variety to be found among different types and brands of sake. And these watches feel special to me, and distinct from anything else Grand Seiko has done so far – maybe thanks to the fact that I have been able to see one of the few working forges in existence in Japan where swords are still made the same way that they have been for centuries.

On the day of our visit to Yoshindo Yoshihara’s forge, we admired a completed katana in the living room of his home – he allowed me to handle it which was slightly scary since it was basically a four foot long straight razor –and then we walked through a small garden to the forge, which was an unassuming structure near the rear garden wall, dark inside and lit only by what light came in the doorway, and the glow of coals in the forge itself. Yoshihara’s family has been making katana for ten generations which is an impressive feat of consistency (my older son, who is a genealogy fan, tells me that a branch of the Forsters from which he claims we are descended, use to hold Bambergh Castle ten generations ago, until one of us took the wrong side in the Jacobite rebellion, so we haven’t exactly maintained old family traditions in quite the same way).
Inside the forge, sweltering in the summer heat, three apprentices dressed in traditional hakama had lit the fires and were beginning the process of heating and folding a billet of steel destined to become a katana. In the gloom, the heat of the forge, roaring rhythmically as one of the apprentices worked the bellows, brought a billet of steel to a red-white glow, and two apprentices – one working a hammer, and one holding the billet – began the long process of turning the raw steel into one of the most obsessively refined pieces of craftsmanship in the world. As the hammer struck the billet, a shower of sparks flew over and over into the darkness and you could easily imagine that you had been transported back hundreds of years. I watched, fascinated, until our tour guide broke the spell.
“We can leave now,” she said. “They will do this for three days.”
For specs and pricing, find out more at Grand Seiko USA. You can find out more about Yoshindo Yoshihara here, but be warned if you covet one of his blades, that in another striking parallel to the watch world, his waiting list is currently closed due to a large backlog of orders.